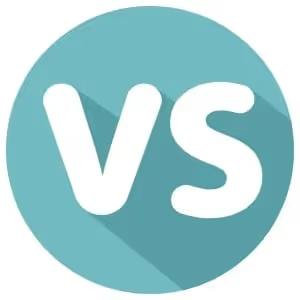
The pharmaceutical industry is fraught with competition, as new products with flashy benefits are continually developed. To sort the good from the not-so-effective, pharmaceutical manufacturers can measure drug effectiveness by its ability to achieve the intended effect; this is strongly influenced by the bioavailability of active pharmaceutical ingredients (APIs). Production of pharmaceutical products is commonly undertaken by wet milling or high pressure homogenization. Both are milling techniques that produce nanoparticles, and both can improve API bioavailability. So which technique will be the best fit for your product?
Wet Milling
The most common method of producing nanoparticles, wet milling is a more effective milling technique than the well-known dry milling. Media milling is known as the ‘classical’ wet milling technique; this process treats a dispersion of concentrated drug in an aqueous or non-aqueous liquid medium with milling balls. The process is advantageous in its economic value and ease in scaling up. However, there are also significant drawbacks to this method. Due to intensive mixing forces in the vessel, erosion of the mill balls is a common occurrence. The erosion residues increase the likelihood of product contamination, which can affect the product’s chemical makeup and function. Impurity levels of the final product must therefore be carefully monitored. (1)
High Pressure Homogenization
As described above, wet milling and high pressure homogenization are similar in significant ways. Both processes can achieve small particle sizes and offer clear economic advantages and opportunity for scale-up. However, the technique for each is distinct. As compared to wet milling, high pressure homogenization reduces a sample’s particle size when it is forced through a narrow tube at incredibly high pressure. The settings on a homogenizer are oftentimes customizable, so a scientist would be able to optimize the process for each drug product. And finally, because high pressure homogenization doesn’t use mill balls, contamination of the final product is much less likely; this is a clear advantage, as contamination confers increased cost and time requirement.
Pion: Homogenizers for Nanoparticle Production
Production of nanoparticles, as seen above, requires powerful mixing equipment that will enhance the bioavailability of APIs. Homogenization is the preferable method due to its ability to reduce particle sizes more significantly than other blending/emulsification methods. (2) The first step in synthesizing a high quality nanoparticle is purchasing equipment that will achieve small and consistent particle size distribution. One such example is the high pressure homogenizer by Pion. Our products are trusted by pharmaceutical researchers and lab managers around the world for key benefits, such as production of nano/micro emulsions, dispersions, and suspensions; importantly, this equipment can achieve consistent particle sizes at or below 100 nm, a key benefit for researchers & corporations that synthesize pharmaceutical products.
In addition, Pion has extensive experience assisting its product users as they transition through the drug development process. Our homogenizers are differentiated for R&D, clinical trials, and manufacturing, and our customer support is reliable, experience-driven, and effective.
Learn more by checking out our pharmaceutical processing equipment.