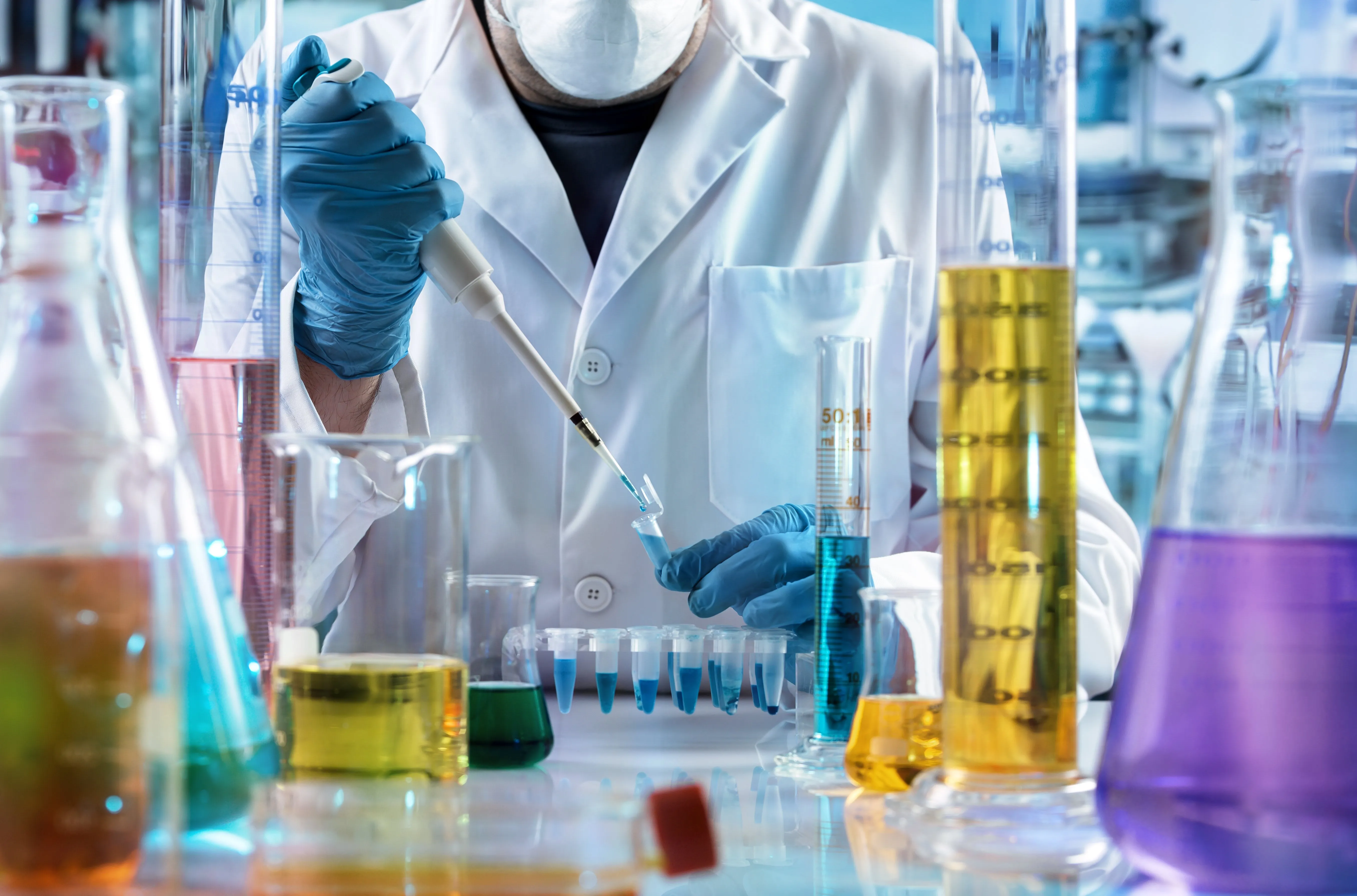
Cavitation is the rapid expansion and implosion of vapor-filled bubbles (or “cavities”) within a liquid substance. These cavities form when intense vibration within the liquid breaks its natural bonds and causes its ambient pressure to become lower than its vapor pressure. In many instances, cavitation is seen as a problem, causing functional changes in both natural and manmade processes that make reliable and consistent operational results impossible. In other cases, however, cavitation can be harnessed for specific manufacturing benefit, delivering products that are more effective — in both application and cost — than those made without it. Chemical engineers, for example, rely on cavitation to homogenize particles within colloidal suspensions, thus enabling them to create a wide range of chemical products including polymers, plastics, pigments, paints, pastes, pharmaceuticals and more! Read on to learn how cavitation is used in chemical engineering:
Cavitation is Used to Reduce Particle Size
In many (perhaps even most) chemical manufacturing processes, substances need to be mixed in order to be useful. Thus, first and foremost, cavitation is used in chemical engineering as a way to reduce particle size so that one substance can be more thoroughly combined with another one. Think about it: it’s a lot easier to combine small, uniform pieces than it is to combine large, various-sized ones!
Cavitation is Also Used to Improve Cohesion
Furthermore, smaller particles mean more surface area; more surface area means more opportunities for particles to interact with one another; and more interaction ultimately yields better — i.e., tighter — cohesion. Because of this, the implosions caused during cavitation inception can be intentionally harnessed during chemically engineered product processing as a way to disrupt the natural bonds of a substance, creating products with a tight distribution of smaller particles that subsequently improve their consistency, viscosity, texture, appearance and even bioavailability (when applicable)!
Indeed, the uniformity of particle size and the cohesion it facilitates combine to provide enhanced product stability, ensuring more effective and a lot longer lasting products than those created in other ways.
The Pion Advantage
In the chemical engineering world, cavitation isn’t just a problem to be avoided, eroding pumps and interfering with mechanical operations. On the contrary, cavitation can be used for advantage in many chemical manufacturing processes; intentionally initiating cavitation during production allows manufacturers the ability to create extremely effective, reliable and shelf-stable products. And if they use a Pion BEE brand high pressure homogenizer, the results can be further compounded.
Want to Learn More?
Our proprietary emulsifying cell technology ensures the scalability and customizability of all types of chemical processing, benefits a lot of equipment used to induce cavitation on the market today can’t guarantee, as well as requires fewer passes of product to deliver maximum effect, saving companies time and money. Finally, the high pressure with which our homogenizers operate destroys potential pathogens, ensuring that all products made with our homogenizers are safe and free of biological contaminants. To learn more about the advantages of using Pion's BEE brand of high pressure homogenizers to induce cavitation during chemical processing, please contact us.