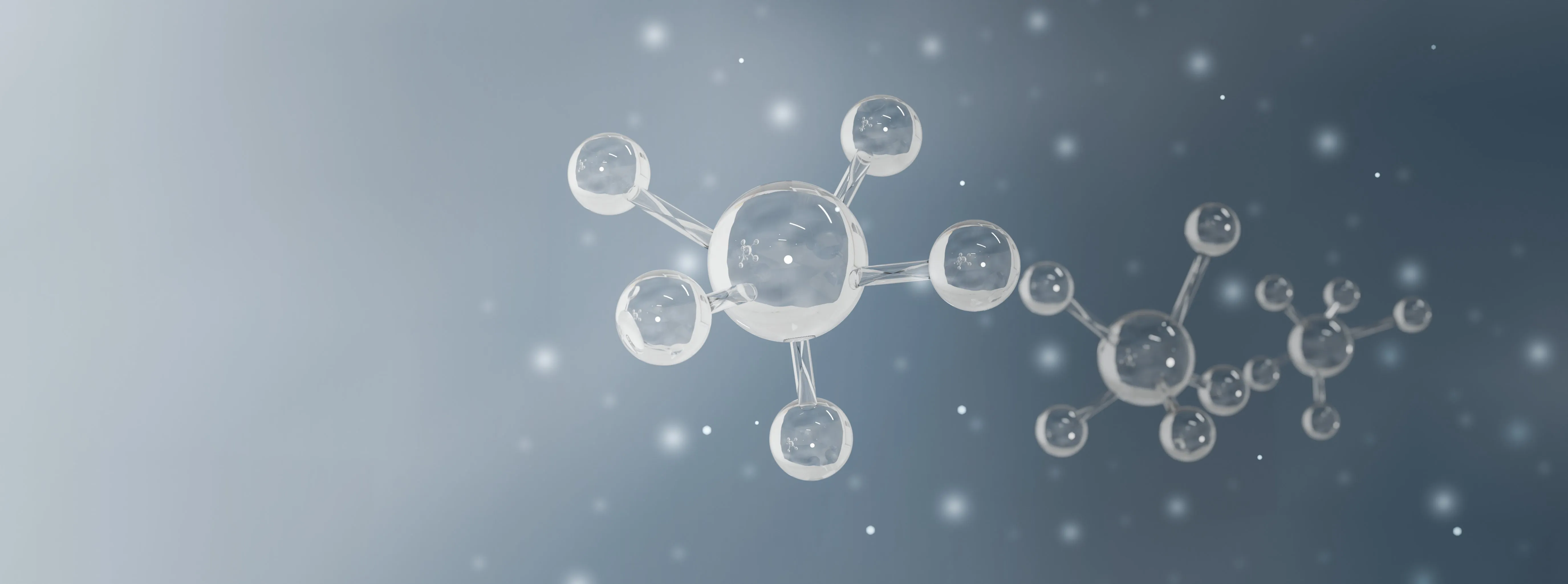
The ability to manufacture quality products depends on the quality of the materials. And quite often the best materials are the ones with a consistent size and distribution of their particles. That’s because the stable distribution of particles directly impacts the physical and chemical composition of the materials they compose, affecting the ability of those materials to function as needed when coming off a production line. Take a look at three materials where particle size is especially essential for effective production:
Food
Today, the majority of the food we eat is manufactured in some way. It has been altered from its natural state to satisfy safety and storage standards and to provide consumers with reliable products that are good to eat every time we purchase them. In many — probably most — of those instances, manufacturers have had to combine several ingredients in order to make these products. Items such as milk, salad dressings, juices, coffee, flour, chocolate, spices and more rely on equipment that reduces at least one of their ingredients to a very small size because breaking particles into smaller-sized pieces increases the surface area of each particle and provides more opportunity for chemical bonding to take place. More bonds mean better cohesion amongst all the ingredients and an extended shelf life for the final food product. Indeed, with all ingredients of a food item thoroughly mixed, it simply tastes better and lasts longer, and its flavor remains consistent with every bite! Small particles frequently improve the nutritional value of the food, as well, especially when nutrients need to pass through bodily membranes and/or preservatives need to be added to food to keep it safe for consumption. Small particles mean the preservatives are not visibly noticed or tasted and the food is still nutritious and safe to eat.
Take, as an example, milk. When smaller in size, the fat globules in milk stay more evenly dispersed; they don’t float to the top of the milk and settle into a layer of cream. They are also easier to digest when they are smaller, meaning the body is able to more quickly access the milk’s nutrients and put them to use to keep us healthy.
Pharmaceutical Ingredients
Particle size is similarly important in the manufacturing of drugs and pharmaceutical products including but not limited to injectables, tablets, sublingual dissolvables, dermal patches, and creams. By reducing the particle size of the chemical components or “API” within pharmaceutical formulations, it allows them to be easily absorbed by the body, enhancing bioavailability. As pharmaceutical products must meet reproducible standards for drug delivery in both efficacy and dosage accuracy, the importance of consistent particle size during production cannot be understated.
Cannabis Products
Traditionally, cannabis and hemp products go through an extraction process where chemical compound rich oil is isolated from plant matter. This oil is considered hydrophobic, which means it does not easily mix with other water-based products. However, by reducing the particle size of the oil droplets and creating a nanoemulsion, it becomes possible to suspend these submicron oil particles in water-based products for prolonged periods of time.
Similarly to pharmaceutical applications, cannabis and hemp products also become more bioavailable through particle size reduction. The human body cannot readily absorb cannabinoid molecules because they are too large to pass through mucus membranes and enter the blood stream. The body first must digest the cannabinoids and THEN absorb them which is why traditional edibles take so long to take effect.
Cannabinoids that have undergone particle size reduction have quicker onset time, are more consistent in active ingredient dosing, have longer shelf life, and are quickly becoming the gold standard method of consumption among users.
The Pion Advantage
Particle size and distribution are important aspects to consider during the manufacturing of thousands of products. Food, pharmaceutical ingredients, and cannabis products are just a few groups where particle size becomes critical for ensuring stability, consistency, and effectiveness. One of the most efficient and scalable ways to guarantee a tight particle size distribution across the widest array of industries is through high pressure homogenization.
Pion manufactures top of the line high pressure homogenizers that provide unparalleled process control and allow the user to manipulate all three forces involved in high pressure homogenization (Shear, impact, and cavitation) for extensive formulation discovery and efficiency optimization.
To learn more about our proprietary Emulsifying Cell (EC) technology, please contact us today.