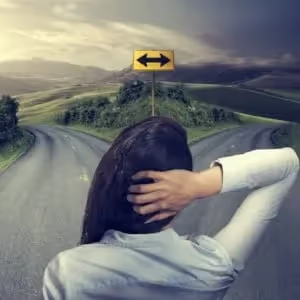
It’s not uncommon for terms or even buzzwords in various industries to be similar but have different applications. For example, in the healthcare industry, electronic medical and electronic health records may sound the same. However, electronic medical records (EMRs) are a digital version of the paper charts in the clinician’s office that contain the medical and treatment history of the patients in one practice, while electronic health records (EHRs) focus on the total health of the patient, provide a broader view on a patient’s care and are designed to share information with other healthcare providers.
Similarly, though the terms “liquid homogenization” and “high-pressure homogenization” appear comparable, each has its own characteristics and primary uses. Homogenization in general can be defined as the reduction of particle size of any given molecule and is a process utilized often in the pharmaceutical, biotech, cosmetic and pharmaceutical industries. Its benefits include more even particle distribution, improved texture and enhanced appearance and taste.
Liquid homogenization, achieved by using a liquid mixer, and high-pressure homogenization offer similar outcomes yet use distinct processes. The mixing processes and mixer designs chosen are determined by the nature of the materials to be mixed. Essentially, the type of product you select for your laboratory depends on its downstream applications and the cell types being used.
In this blog, we’ll describe the differences between liquid and high-pressure homogenization and list pros and cons of each to help you decide which one is best suited to your business needs. Whichever you choose, it’s important that it has the flexibility to meet the various needs of a laboratory.
Liquid Homogenization
Widely used for cell disruption of cultured cells and small sample volumes, liquid homogenization requires a sample to manually be forced through a narrow space, thereby shearing membranes and decreasing particle size. There are three most common types of liquid mixers used: the Dounce homogenizer (used for gently lysing single cell suspensions), Potter-Elvehjem homogenizer (used with delicate tissues) and the French press (used for small sample volumes). In addition to being suitable for operation at higher temperatures and easy to maintain, liquid mixers offer enhanced repeatability and a lower power requirement. Nevertheless, the throughput from all three models is fairly low, and they may not provide enough scalability.
High-pressure Homogenization
Utilized for numerous products from the chemical and biotechnology industries and products such as pharmaceutical tablet coatings, vaccinations and creams, high-pressure homogenization uses multiple mechanical forces (such as turbulence, cavitation and shear) along with intensive pressure to achieve micronization and membrane lysis. Similar to liquid mixers, high-pressure homogenizers work by forcing cell suspensions through a very narrow channel under pressure. Unlike the manual requirement of liquid homogenizers, though, high-pressure units run automatically and are often made to be scaled from laboratory experimentation to manufacturing.
Benefits of high-pressure homogenization include an increased rate of dissolution, ease of operation, cost and time effectiveness, consistency in composition of products, greater stability of final products due to a stable emulsion and upgraded scalability and repeatability. High-pressure homogenization also has the ability to reduce particle size to levels that are not achievable by most other mixing processes. Because they tend to be large and very heavy, high-pressure homogenizers are typically used for large volume processing and consume more power than liquid mixers. They sometimes require more complex cleaning, cannot handle large particles or high-fiber materials and aren’t the most suitable for high temperature materials.
Pion: The Industry Leader in High-Pressure Homogenizers
Pion offers a wide variety of BEE brand high-pressure homogenizers to meet the needs of virtually any industry. Unlike liquid mixers, our homogenizers are suited for large samples and offer large throughputs, making them ideal for laboratory, pilot plant and even industrial use. In addition, our easy-to-use equipment produces higher yield in less time and utilizes multiple forces – shear, turbulence, impact and cavitation – to allow for results that are reliable, repeatable and high quality.
There are plenty of companies on the market to select equipment from; however, the product can be of higher quality and more even consistency when run through top-shelf equipment, most frequently in the form of a homogenizer. Pion is trusted by researchers around the world for both our laboratory homogenizers and associated customer support. Learn about how BEE’s products can maximize your homogenization processes by contacting us today.