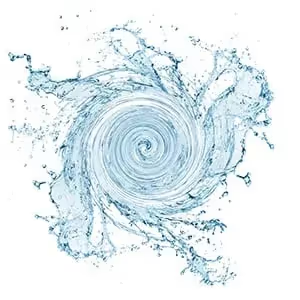
On average, four out of five Americans are prescribed antibiotics each year. (1) This equates to nearly 255 million people using a single pharmaceutical product, and does not take into account the many other products being used on a regular basis! To maintain consistent product availability, pharmaceutical manufacturers must have optimized mixing processes to achieve timely and efficient production. Following is a compilation of factors that can be adjusted on most homogenizers, which can optimize the mixing process and ultimately the product that will go to market.
- Pre-Mixing Treatment
Products tend to yield better results when heated prior to mixing; this is largely due to the effects of elevated temperature on viscosity, surface tension, and ability to aid the emulsification process. However, some products may actually fare better from pre-cooling; the optimal temperature is product-specific and should be tested in trial runs before experimentation.
- Reverse Flow vs. Parallel Flow
Reverse flow confers product-on-product shear and allows for more impact, which is optimal for disruption of cells with thick walls that are not easily penetrated. Parallel flow, on the other hand, confers product-on-equipment shear, a shorter process, and less impact so as not to disrupt intracellular components. Additionally, parallel flow provides less shear than reverse flow.
Most homogenizers offer either pattern; although both EC setups should produce good results, one might yield better results depending on the product and application. When you first run a product through the homogenizer, try it both ways to see which provides a better outcome.
- Operating Pressure
Reduced particle size is a measurable and successful outcome of the mixing process; increased operating pressure typically equates to decreased particle size. High quality homogenizers, such models produced by Pion, can achieve a maximum operating pressure of 45,000 PSI.
- Number of Passes
Multiple homogenizer passes are frequently employed to achieve complete cell disruption and/or smallest possible particle size; case studies have shown that with each pass, a smaller particle size is achieved. (2) Pion homogenizers are among few on the market that can achieve particle sizes of 0.1 µm after only one pass.
- Post-Mixing Treatment
Whereas elevated temperatures are recommended for pre-mixing treatment, when mixing has concluded the product temperature should be reduced immediately. This step is in place largely because elevated temperatures are detrimental to product stability; as such, some homogenizers contain a heat exchanger to quickly reduce temperature after mixing.
When you are ready to mix a product for the first time, run a few trials first. Determine what you are looking for: Smallest possible particle size? Disruption of a thick-walled cell? Then make adjustments to each of the above factors to identify the combination that will give your product optimal results.
Do you have a product that requires mixing but don’t have the proper equipment? Pion offers homogenizers with the ability to adjust all 5 factors in this post, which will help your lab produce nano/micro emulsions, dispersions, and suspensions. Visit us here to learn more about our products.