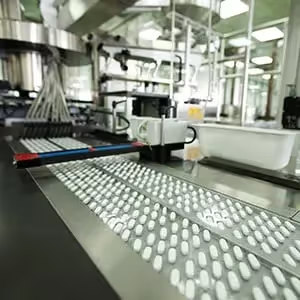
The 10 largest pharmaceutical firms in the world reported profit margins of up to 43% in 2014, an astounding margin for any company across industries. Of this, a significant portion was derived from drug tablet sales. Every aspect of a given tablet, from active ingredient to excipient to overall taste and ease of consumption must therefore be considered; in particular, tablet coating is a critical consideration due to its impact on these factors. Following is a compilation of frequently used tablet coatings and their composition.
Sugar Coating
The oldest existing coating technique, sugar coating was widely used until development of the film coating in the 1950’s. Application of sugar coating involves deposition of sucrose-based compounds from aqueous solutions, and is multi-staged; the process includes sealing, sub coating, smoothing, coloring, polishing, and printing. Sugar coating is preferred for its ability to mask unfavorable taste and thick coating that prevents moisture and light from affecting the drug’s stability. However, significant disadvantages include the 30-50% weight increase due to coating material and the labor/time required of its multi-step process. (1)
Film Coating
More frequently used than other coating varieties, film coating was developed as a tablet size-reducing alternative to sugar coating. Film coating is characterized by application of an excipient suspension formulation, consisting of polymer, plasticizer, colorant, and solvent, directly onto the tablet. The overarching purpose for each ingredient is either around safety and feasibility for industrial production/application or stability and taste for the consumer.
Enteric Coating
Classically applied to oral medications, the ‘gastro-resistant’ coating has two central purposes: 1) Protects a drug from the high acidity of stomach contents, which is necessary if its destination is distal to the stomach, and 2) Protects the stomach from a drug, particularly from stomach ulcer-causing drugs like aspirin and naproxen. The chemistry of enteric coatings is triggered by pH; the low-acidity environment of the small intestine facilitates its breakdown, whereas it is resistant to the high acidity of the stomach. This type of tablet should never be crushed or diluted down before ingesting. (2)
Compression Coating
Most drugs that are compression-coated contain two insoluble materials separated into two parts. The outer coat is typically a water-soluble sugar compound and dissolves after swallowing; the internal core usually contains an enteric coating that allows for a second drug release during a later digestive stage. Depending on the drug, however, the internal core may be liquid to allow for simultaneous release with the outer coat. (3)
Tablet Coating Production (All Types)
Regardless of which coating type your pharmaceutical drug requires, you will likely need access to specific lab equipment and reagents. In particular, a homogenizer that can achieve the vigorous mixing and granular dissolving required of high quality coatings is key. Use of a high quality homogenizer can have downstream effects for the consumer, including ease in swallowing, visual attractiveness, and appropriate internal release.
At Pion, we produce homogenizers that can yield a variety of relevant products, such as emulsions, suspensions, dispersions and lipids. Importantly, these products and more are incorporated into the tablet coatings described above. In addition, Pion has extensive experience assisting its product users as they transition through the drug manufacturing process.
Visit Pion here to learn more about how their homogenizers can help you synthesize a high quality tablet coating.